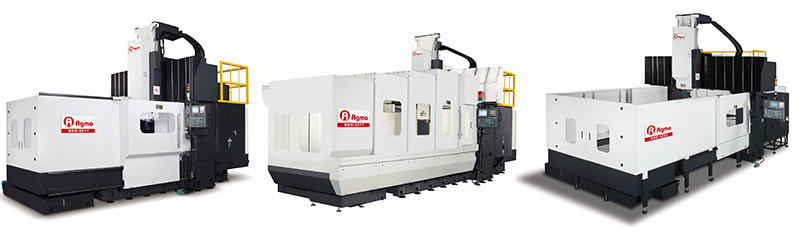
BDO-SERIES High-Rigidity, High-Precision & High-Efficiency Design Concept
![]()
![]()
![]()
![]()
![]()
|
Double Column Vertical Machining Center | |
![]() |
![]()
|
![]() |
![]()
|
Perfect Structure Design
High Quality Guarantee
![]()
|
![]()
|
![]() |
Different Types Of Spindles Are Available | |
![]() |
![]() The gear-driven spindle provides spindle speed of 4,000rpm and 6,000rpm with high output torque which is the best choice for frequent heavy-cutting operations. |
![]() |
![]() ZF spindle has higher torgue than belt-driven spindle. ZF spindle provides higher rotational speed than gear driven does. ZF gear box has 1:4 speed reduction ratio mechanism. It enlarges output torque by 4 times. It offers an extra choice for users who needs high rotation speed and high torque for machining operation. |
![]() |
![]() The design of the back holder of cross-beams neatly aligns hydraulic unit, cooling machines, and spare parts, etc., and meets the requirement of CE regulations. This design offers two advantages: 1. More free spaces for operators 2. Easy to maintain |
![]() ![]() |
![]() Spindle speed:6,000rpm. BT-50 taper adopts short spindle end design with use of gear box. This is suitable for heavy cutting. Spindle torque could reach 572Nm, and 8,000rpm spindle is available. ![]() The design of the extended long-end spindle is especially suitable for deep hole machining. BT-50 inside hole taper and 6,000rpm spindle are standard design. 8,000 rpm spindle is available. It is very suitable for large mold machining. ![]()
|
Standard Accessories–Complete In Every Line | |
![]() |
![]() |
32 TOOLS ATC | OIL CIRCULATING COOLING SYSTEM FOR SPINDLE |
![]() |
![]() |
X-AXIS TWIN CHIP SCREWS ON TABLE SIDES | EXCHANGE TOOL ARM |
![]() |
![]() |
FOOTSWITCH FOR TOOL UNCLAMPING | AUTOMATIC LUBRICATION SYSTEM |
![]() |
![]() |
GAS STORAGE TIN | HEAT EXCHANGER FOR ELECTRICAL CABINET |
All Kinds Of Addition Heads(opt.) |
![]() |
![]() |
30˚ Angular Head |
90˚Angular Head |
Multiangular Milling Head |
Extend Head (300l) |
|
Max. Output Power kw(hp) | 11(15) | 15(20) | ||
Spindle Taper | BT50(7/24) | |||
Max. Rotation Speed rpm | 3500 | |||
Tool Clamping Method | Manual Bolt/Auto Bolt | |||
Index Method | Manual index/ Auto 5-Degree Index/1-Degree Index | No Index |
Option Accessories | |||
![]() |
![]() |
![]() |
![]() |
Auto 90 degree head warehuse beside ATC | Auto 90 degree head warehouse on table | Semi Auto 90 degree head warehouse by swivel arm | 60 VERTICAL HORIZONTAL ATC. |
![]() 1. Belt Driven 6,000 RPM Spindle 2. Three Axis Crashprooof Mechanism 3. X-Axis Circulating Decoder Feedback 4. Twin Hydraulic Counter Weight Cylinder 5. Movable Manual Pulse Generator 6. Centralized Automatic Lubrication System 7. Enclosure Splash Gurd (Without Roof) 8. 32 Tools ATC 9. Flood Coolant System 10. Twin Chip Screw On Table Side 11. RS-232 Interface 12. Chain Type Chip Conveyor 13. Oil Skimmer 14. Quartz Work Lamp & Fluorescent Lamps 15. Program End Warm Lamp 16. Wash Gun & Pneumatic Interface 17. Rigid Tapping 18. Movable Manual Pulse Generator 19. Tool Box (Include One Set Of Tools For Adjustment) 20. Footswitch For Tool Unclamping 21. Foundation Bolts & Adjustable Bolts 22. Maintenance & Operation Manual 23. Controller Fanuc 18iMB |
![]() 1. Gear Driven 6,000 RPM Spindle 2. Belt Driven 8,000 RPM Spindle 3. Enclosure Splash Guard (With Roof) 4. 40 Tools ATC 5. 60 Tools ATC 6. Controller Fanuc OiM 7. 4th Axis Preparation 8. 90° Angular Head 9. Multiangular Milling Head 10.Extend Head- 300L 11.Extend Head- 500L 12.Head Warehouse 13.Linear Scale Feedback System For X,Y,Z Axes 14.Auto Tool Length Measurement 15.Auto Work Piece Measurement 16.Coolant Through Spindle A Type(20/70 bars - Closed Hole) 17.Coolant Through Tool 18.Z Axis Travel 800mm |